Poured Walls vs. Block Walls: Which Is Stronger, Cheaper, and Faster for Commercial Construction?
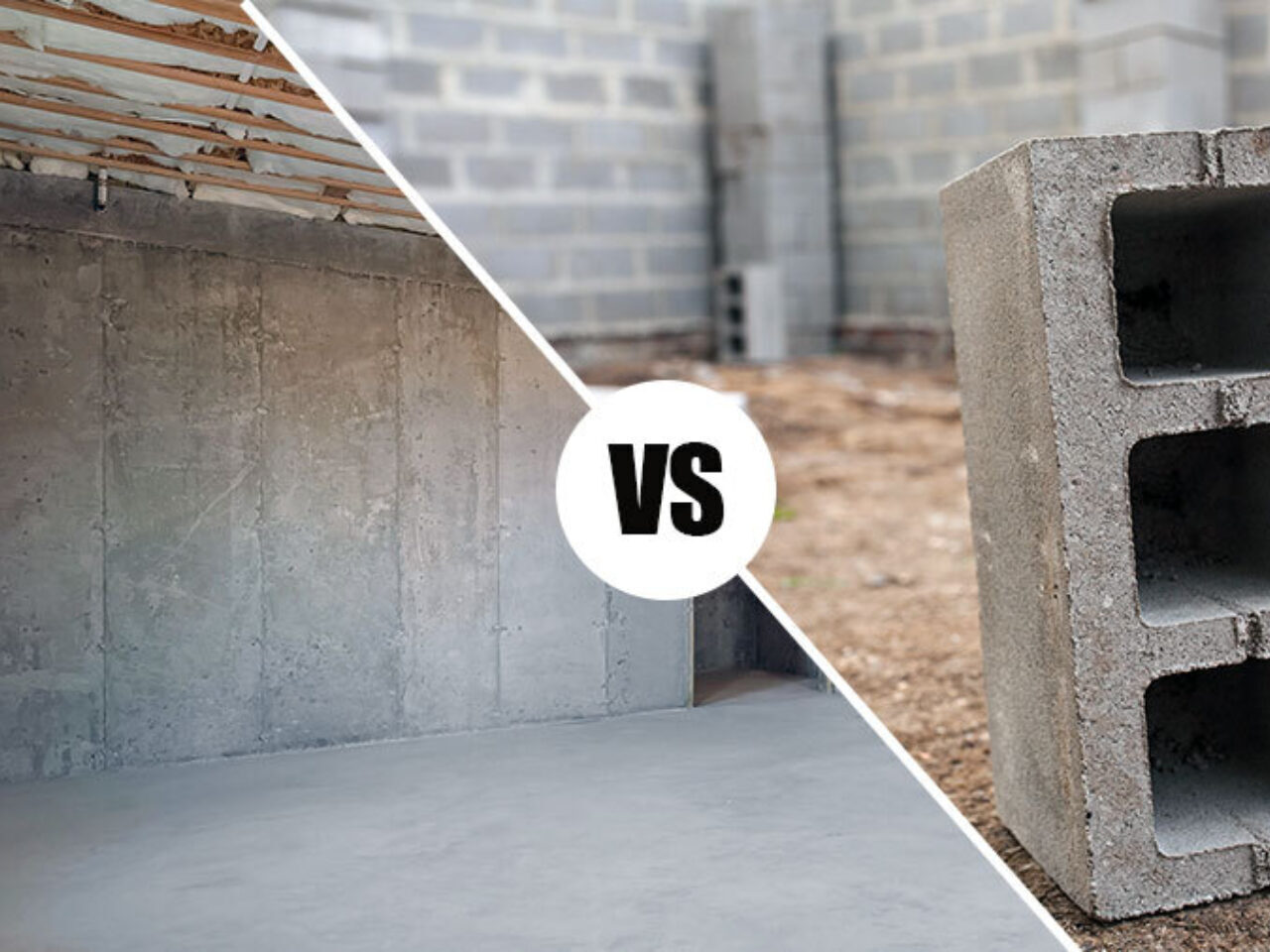
When you’re planning a commercial building, the wall system you choose plays a major role in how strong, fast, and cost-effective the project will be. Two of the most common systems used in commercial work are poured concrete walls and concrete block walls, also known as CMU (concrete masonry units).
Each wall type has its own strengths. Some are better for speed, some for long-term durability, and others for meeting a tight budget. This guide breaks down the pros, cons, and key differences between the two so you can choose the best fit for your facility.
IN THIS ARTICLE:
What Exactly Are Poured and CMU Walls?
Wall Strength Comparison: Which Option Holds Up Best?
Budget Check: Is Poured Concrete or CMU More Cost-Effective?
Time on Site: Which Wall System Builds Faster?
Waterproofing Matters: Which Wall Stays Dry Longer?
Flexibility and Future Modifications
Thermal and Fire Performance
Aesthetic Differences: Appearance and Finish Options
When Poured Makes Sense—and When Block Wins Out
Final Thoughts: What’s the Right Choice for You?
What Exactly Are Poured and CMU Walls?
Poured Concrete Walls (Cast-in-Place)
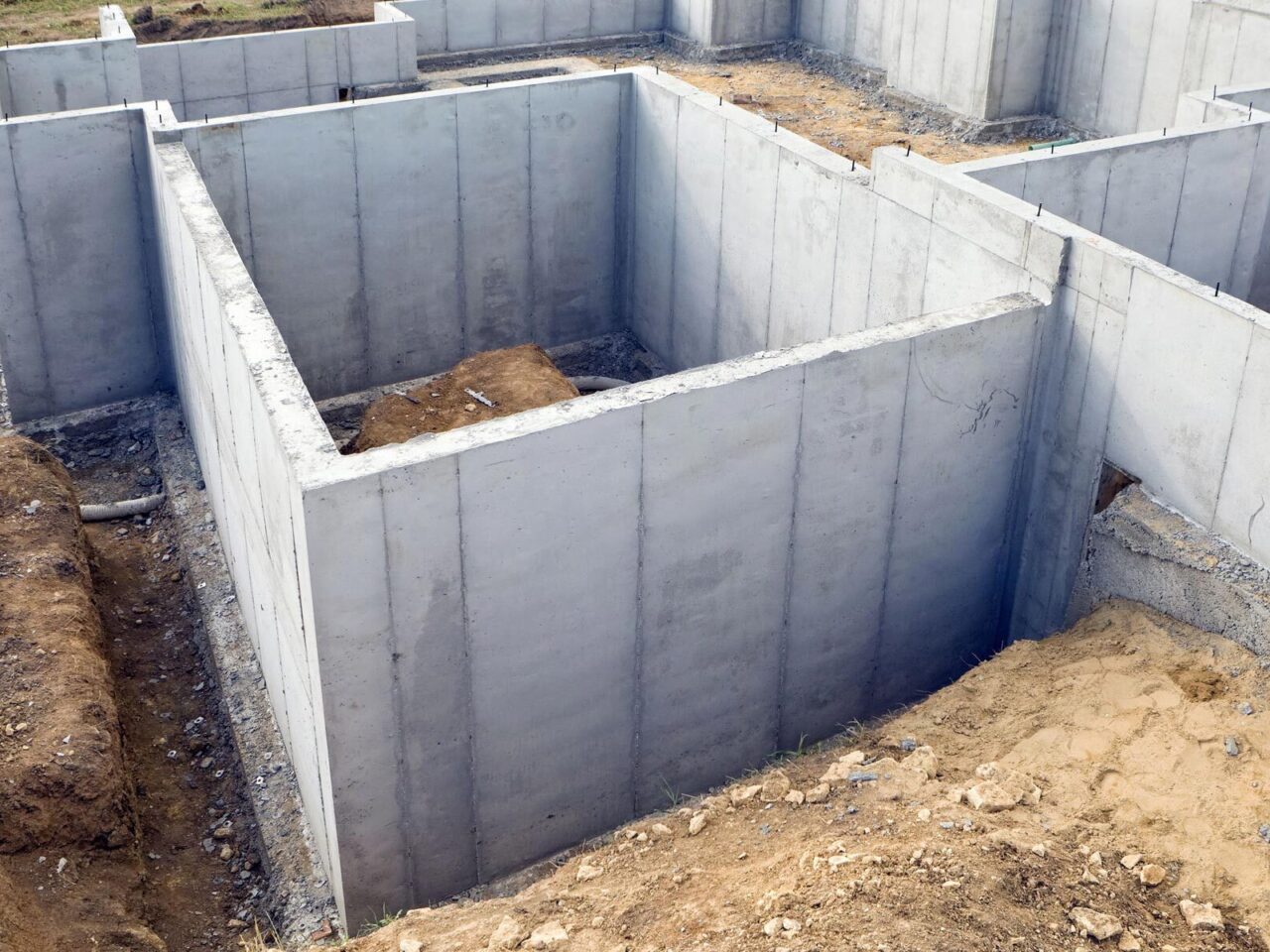
Poured walls are made by setting up forms, placing steel reinforcement (rebar), and then pouring concrete directly into the forms. Once cured, the concrete forms a single, solid wall with no joints or seams.
This type of wall is often used for:
Commercial foundations
Retaining walls
Exterior walls in industrial buildings
Walls that need to resist water or soil pressure
Tall structures where jointless construction matters
Concrete Block Walls (CMU)
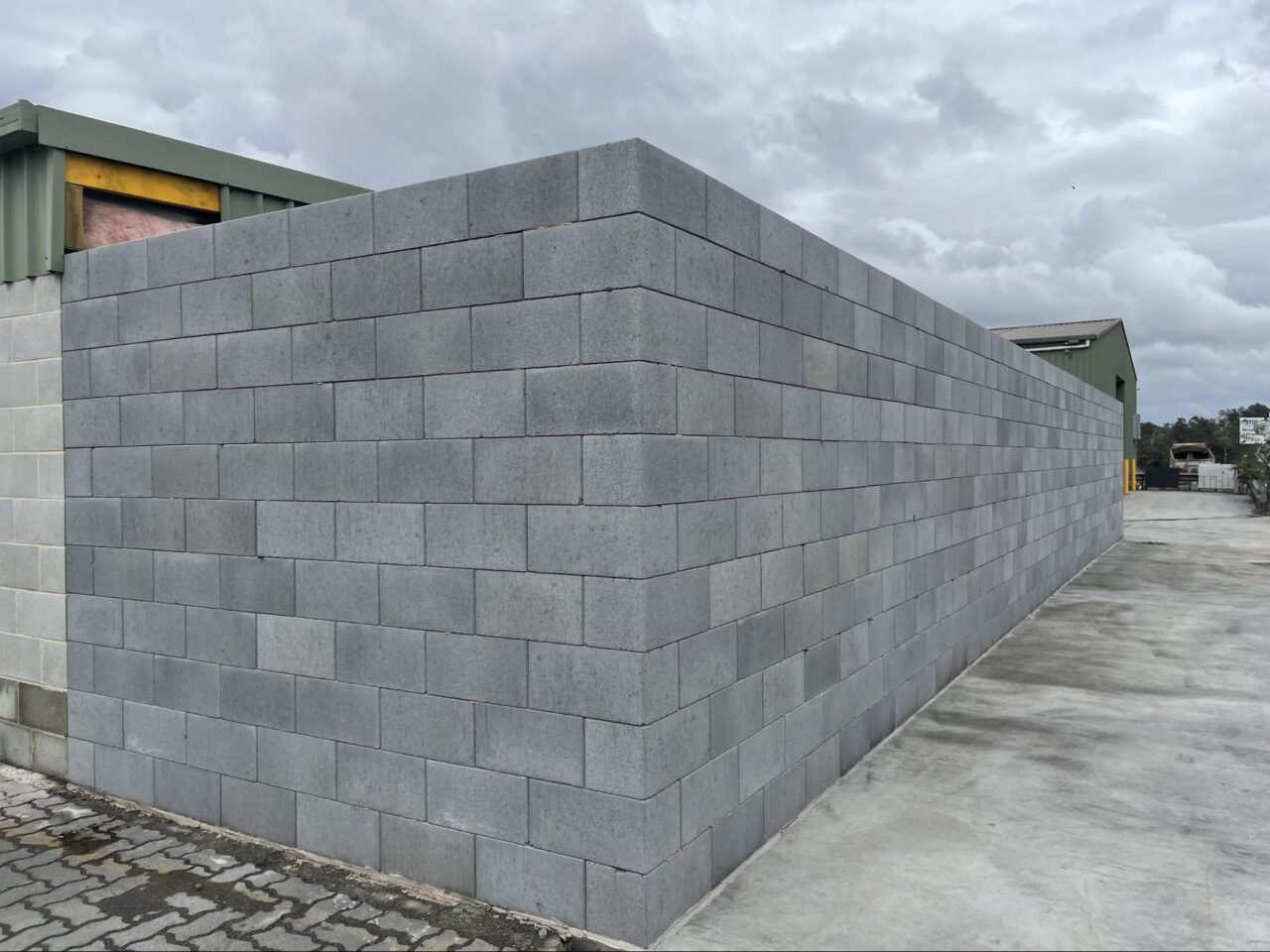
Block walls are built by stacking individual concrete blocks (usually 8"x8"x16") in rows. Steel bars are inserted vertically and sometimes horizontally, and grout is poured into the hollow block cells to improve strength.
Common use cases include:
Warehouses
Partition walls inside large buildings
Fire-rated walls between building sections
Facilities that are built in stages or phases
Wall Strength Comparison: Which Option Holds Up Best?
Both wall types are strong, but they perform differently under certain conditions.
Poured Walls
Higher lateral strength: Great at holding back soil or resisting wind pressure
Fewer cracks: No joints means fewer places for cracks to form over time
Better waterproofing: Less prone to leaks or seepage
Stronger in seismic zones: Performs better during shifting or movement
Block Walls
Good compressive strength: Still strong when built properly with rebar and grout
Effective for short walls: Works well for standard-height commercial walls
Fire-rated: Provides good fire resistance in many building types
Easier to modify: Can cut in doors, windows, and mechanical openings more easily
Overall, poured walls offer better long-term durability and performance, especially in heavy-duty or below-grade applications. CMU walls are strong too, but require more maintenance and may not last as long under high pressure or wet conditions.
Budget Check: Is Poured Concrete or CMU More Cost-Effective?
Cost can vary depending on the project size, wall height, labor rates, and material pricing.
Cost Factor | Poured Walls | Block Walls (CMU) |
Materials | More expensive — needs forms, concrete, rebar | Less expensive — blocks are factory-made |
Labor | Requires skilled crews and concrete equipment | Less technical labor, no pump trucks |
Install Speed | Faster for large sections | Slower overall, but easier in small areas |
Maintenance Over Time | Very low — few repairs needed | Higher — mortar joints can crack or wear out |
Average installed cost per square foot (commercial work):
Poured Walls: $16 to $22
Block Walls: $12 to $18
Block walls may cost less at first, but poured walls may save money in the long run due to lower repair and maintenance needs.
Time on Site: Which Wall System Builds Faster?
Construction timelines matter. Here’s how each system stacks up.
Poured Walls
Faster for large or continuous wall sections
Once forms are placed and rebar is tied, the wall can be poured in a single day
Requires curing time before follow-up work
Less disruption once complete — no joints to maintain
Block Walls
Slower overall — built block by block
Easy to start and stop — good for projects done in phases
No cure time needed — can move on to finishes or framing faster
Delays more likely in bad weather due to manual labor
If you’re building large foundations or tall exterior walls, poured concrete usually finishes faster. For small jobs or buildings done in pieces, block can be more flexible.
Waterproofing Matters: Which Wall Stays Dry Longer?
For commercial buildings, keeping water out is key—especially in foundations, basements, or storage areas.
Poured walls resist water better due to fewer joints and solid construction.
Block walls can let moisture in at joints if not sealed properly. They often need surface coatings, drain tile systems, or vapor barriers to stay dry.
Poured walls are the clear winner for waterproofing, especially in wet or below-grade conditions.
Flexibility and Future Modifications
In some commercial projects, flexibility matters—especially if future changes or expansions are expected.
Block walls are easier to modify. Openings for doors, windows, or utilities can be cut in with less effort.
Poured walls are harder to alter once built. Cutting into them requires special tools and can affect structural integrity.
If your layout may change over time, or if access to MEP systems (mechanical, electrical, plumbing) is important, block walls might offer more long-term flexibility.
Thermal and Fire Performance
Both systems can meet energy and fire codes, but the details vary.
Neither wall type is highly insulated on its own — both need added insulation to meet commercial energy codes
Block walls often meet 1- to 4-hour fire ratings with standard designs
Poured walls can also be fire-rated with the right thickness or added fire-resistant coatings
Fire and energy performance typically depend more on how the wall is finished and insulated than the wall type itself.
Aesthetic Differences: Appearance and Finish Options
- Poured walls offer a clean, smooth finish that’s ready for coatings, paint, or architectural reveals.
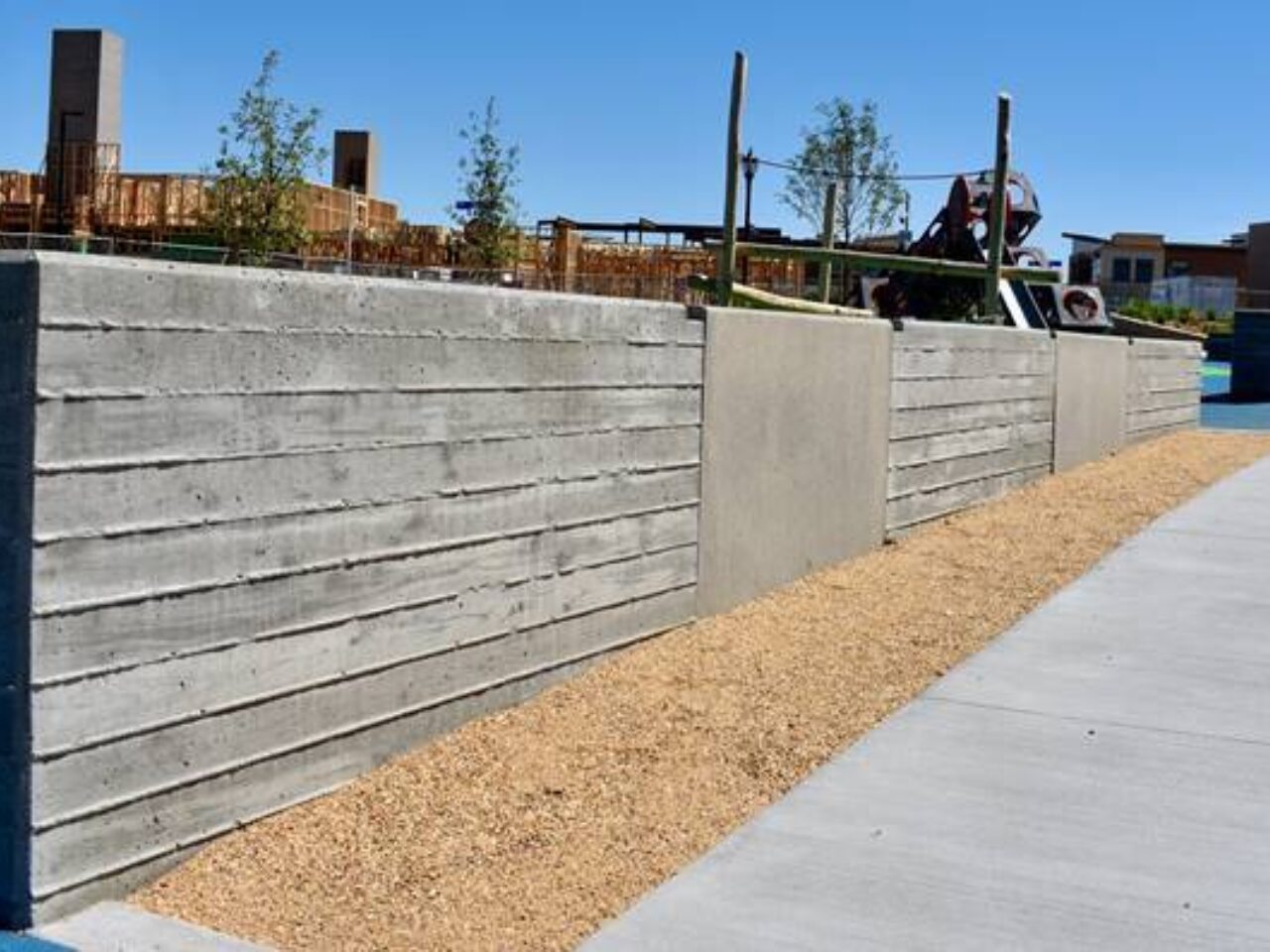
- Block walls have a rougher texture but can be finished with paint, stucco, veneer, or decorative block patterns.
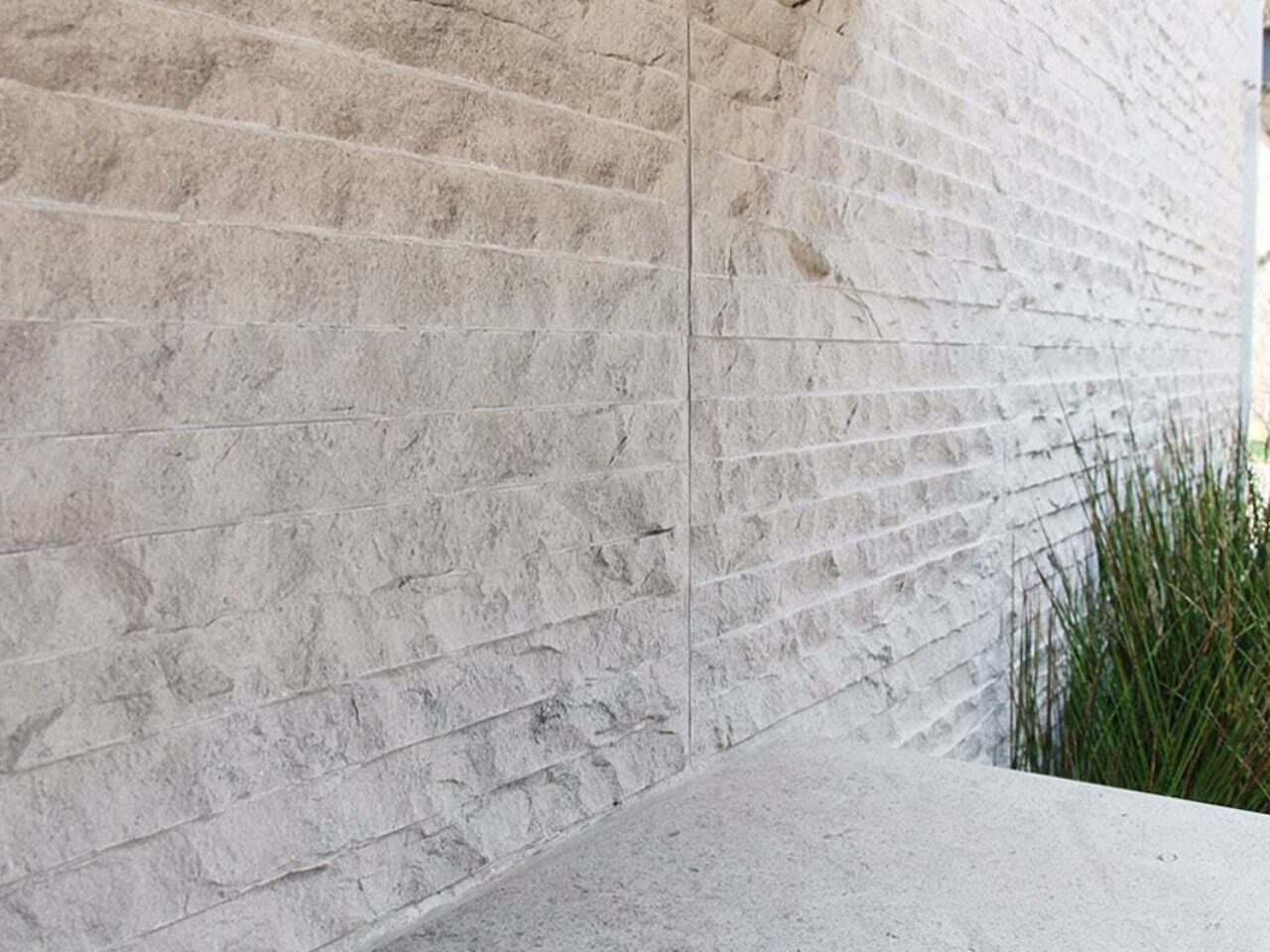
In visible areas like lobbies, entryways, or exterior facades, poured walls allow more architectural flexibility. In back-of-house or warehouse spaces, block is often good enough and cheaper to finish.
When Poured Makes Sense—and When Block Wins Out
Here’s a quick guide to help choose the right wall type based on your project goals:
If your project requires… | Choose… |
Long spans or high structural loads | Poured |
Waterproof or below-grade performance | Poured |
Fast wall construction on large builds | Poured |
Tight budget for smaller structures | Block |
Easy future changes or cut-ins | Block |
Interior partitions or fire separation walls | Block |
Smooth architectural finishes or exposed concrete | Poured |
Final Thoughts: What’s the Right Choice for You?
Both poured walls and block walls are reliable options for commercial buildings. The right choice depends on your project size, wall height, timeline, and budget.
Poured concrete walls are best for strength, durability, speed, and moisture resistance.
Block walls are better for lower-cost projects, flexible layouts, and interior spaces.
Working with an experienced builder or general contractor will help ensure your wall system matches the specific needs of your building. The most important thing is understanding your priorities—so you can build smart from the ground up.